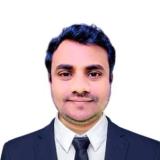
Dantukurti
Plant Manager & Production Manager & Quality Manager & Nutrition & Operations-Nutrisco-ETG-Group
Male33 y/oQuality Management Director/Manager/Supervisor/Factory Director/VP of Operations/Chief Operating Officer/Assistant General Manager/General Assistant (Executive Level)/Other senior management/Product Manager/Quality Management/Laboratory Manager/EngineerLive in IndiaNationality India
Share
Work experience
Plant Manager & Production Manager & Quality Manager & Nutrition & Operations-Nutrisco-ETG-Group
ETG-Group-Nutrisco2022.01-Current(4 years)Ethiopia** *Plant Manager* 1. Developing and executing plant policies and procedures that align with the company’s goals. 2. Ensuring all operations comply with health, safety, and environmental regulations. 3. Directing and managing plant operations for production, maintenance, quality, and shipping and receiving. 4. Oversee daily plant production operations. 5. Enhance production, asset capacity, and flexibility while minimizing costs and maintaining quality standards. 6. Ensure production output, product quality, and on-time shipping. 7. Manage financial aspects, including budget preparation, the Annual Operating Plan, and capital expenditure. Oversee the overall operations of a manufacturing facility, ensuring production runs smoothly while meeting quality, safety, and efficiency standards. Achievements: • Operational Efficiency: Increased plant efficiency by X% through process optimization, implementing Lean/Six Sigma methodologies, and reducing downtime. • Cost Reduction: Reduced operational costs by X% through waste reduction initiatives, improved resource utilization, and better energy management. • Safety Improvement: Achieved a X% reduction in workplace accidents by enhancing safety protocols, training, and implementing safety audits. • Production Capacity Expansion: Successfully increased plant capacity by X% without major capital investment by optimizing workflows and upgrading machinery. • Maintenance Program: Developed and implemented a predictive maintenance program, reducing unplanned downtime by X% and increasing equipment longevity. • Compliance & Certifications: Successfully maintained regulatory compliance (e.g., ISO,FDA). • Employee Development: Reduced turnover and improved team performance by launching a skills development program, enhancing employee engagement and morale. *Production Manager* 1. Planning and organizing production schedules. 2. Estimating, negotiating, and agreeing on budgets and timescales with clients and managers. 3. Assessing project and resource requirements. 4. Ensuring health and safety regulations are met. 5. Supervising and motivating a team of workers. 6. Developing and implementing production plans according to business and market demands. 7. Managing human and material resources to meet production targets and quality standards. 8. Coordinating and supervising staff activities, reviewing performance, and initiating corrective actions as required. 9. Ensuring adherence to safety, health, and environmental standards and regulations within the plant. 10. Assessing and improving operational systems, processes, and policies in support of the organization’s mission. 11. Maintaining relationships with key internal and external stakeholders, including suppliers and customers. 12. Preparing and maintaining production reports and personnel records. 13. Overseeing the maintenance, repair, and replacement of plant equipment and infrastructure to reduce downtime and maximize productivity. Oversee day-to-day production operations, ensuring products are made efficiently, on time, and with high quality. Achievements: • Production Efficiency: Increased production efficiency by X% through improved workflows, automation, and lean manufacturing techniques. • On-Time Delivery: Improved on-time delivery rate by X% through better scheduling, resource allocation, and cross-department collaboration. • Cost Control: Reduced production costs by X% by optimizing material usage, minimizing waste, and implementing energy-saving initiatives. • Quality Control: Reduced defects and rework by X% by introducing stricter quality checks and preventative measures within the production process. • Waste Reduction: Reduced material waste by X% through the introduction of waste-reduction practices or better inventory management. • Capacity Utilization: Increased production capacity by X% through optimized scheduling, better machine utilization, or introducing new machinery. • Safety & Compliance: Improved safety protocols and compliance, achieving zero safety incidents over the course of X months/years. *Quality Manager* 1. Understanding customer needs and requirements to develop effective quality control processes. 2. Devising and reviewing specifications for products or processes. 3. Requirements for raw material or intermediate products for suppliers and monitoring their compliance. 4. Ensuring adherence to health and safety guidelines as well as legal obligations. 5. Overseeing and managing all aspects of quality assurance and quality control within an organization. 6. Developing, implementing, and maintaining quality management systems, policies, and procedures to ensure compliance with quality standards and regulatory requirements. 7. Setting quality objectives and targets, monitoring quality performance metrics, and driving continuous improvement initiatives. 8. Working closely with cross-functional teams to optimize processes, resolve quality issues, and enhance product quality and customer satisfaction. 9. Overseeing inspections, testing, and audits to identify and address defects. 10. Analyzing quality data to identify trends and areas for improvement. 11. Developing and implementing solutions like corrective actions (fixing problems) and preventative actions (stoppingproblems before they occur). Ensure that products meet customer expectations and regulatory standards, and they continuously improve quality control processes. Achievements: • Improved Product Quality: Reduced product defects by X% by implementing stronger quality assurance processes and corrective actions. • Customer Satisfaction: Improved customer satisfaction and reduced complaints by X% through rigorous quality testing and process improvements. • ISO Certification: Led the company to obtain or retain key quality certifications. • Quality Audits: Achieved outstanding audit results, passing internal and external audits with zero non- conformance reports. • Process Improvement: Introduced new quality control procedures that resulted in a X% decrease in customer returns or product recalls. • Supplier Quality Management: Worked with suppliers to improve raw material quality, reducing incoming material defects by X%. • Root Cause Analysis: Conducted effective root cause analysis to identify and resolve quality issues, preventing recurrence and saving costs. *Nutrition* 1. Creating animal nutritional regimens and feeding strategies. 2. Investigating animal feeding and NPD development. 3. Assessing what an animal consumes and how its diet affects its health and consumers' health. 4. Assessing the relative nutritional values of various feeds with standards. 5. Supporting the work of agricultural advisers/consultants. 6. Visiting farms and improve BFM (Best farm management) and BFM (Best feed management) 7. Interpreting forage analysis with root cause and right diet. 8. Using specialist computer software to devise diets and produce reports with complies with standards. 9. Working with clients to formulate diets that meet their requirements/objectives. 10. Design least-cost formulations with suitable diet with standards. Focus on ensuring the products meet specific nutritional standards and cater to consumer health trends while maintaining compliance with regulations. Achievements: • Product Reformulation: Successfully reformulated X products to meet new nutritional guidelines without compromising taste or cost. • Health-Conscious Offerings: Launched X new product lines targeting health-conscious consumers, such as products. • Nutritional Labeling: Ensured 100% accuracy in nutritional labeling across all products, meeting all regulatory requirements and improving customer trust. • Customer Feedback: Addressed customer concerns regarding nutritional content and improved product offerings based on feedback. • Health Partnerships: Collaborated with health organizations or influencers to promote healthy eating initiatives, increasing brand visibility and customer engagement. • Regulatory Compliance: Maintained compliance with all local and international nutritional standards, passing all audits and avoiding fines or penalties. *Operations* 1. Oversee daily operations in the Animal feed sector. 2. Develop and implement operational strategies. 3. Manage budgets and ensure cost-effectiveness. 4. Ensure compliance with industry regulations. 5. Analyze and improve operational processes. 6. Manage a diverse team of employees. 7. Work closely with other departments. 8. Ensure products are delivered on time. 9. Overseeing the day-to-day operations of the manufacturing facility. 10. Ensuring that production targets are met, quality standards are maintained, and operational efficiency is optimized. 11. Collaborating with various departments, such as production, logistics, and quality control, to ensure smooth operations and timely delivery of products. 12. Analyzing production data, identifying areas for improvement, and implementing strategies to enhance productivity and reduce costs. 13. Managing a team of supervisors and ensuring compliance with safety regulations and company policies. Responsible for overseeing and optimizing day-to-day business operations, from production to customer delivery. Achievements: • Process Optimization: Improved overall operational efficiency by X% through process redesign, Lean practices, and eliminating bottlenecks. • Cost Savings: Implemented cost-saving measures that reduced operational costs by X% through more efficient supply chain management, automation, or process improvements. • Cross-Functional Collaboration: Fostered collaboration between departments (e.g., production, sales, andquality) to streamline operations and improve service delivery times. • Supply Chain Optimization: Improved supply chain efficiency, reducing lead times by X% and decreasing stockouts or overstocking issues. • Customer Satisfaction: Increased customer satisfaction and retention by improving on-time delivery and customer service responsiveness. • Technology Integration: Led the successful integration of new technology (e.g., ERP, automation tools) to enhance operational visibility and decision-making. • Team Leadership: Developed and mentored a high-performing team, resulting in improved employee engagement, productivity, and retention.Assistant Quality Control (QC) Manager -The water base limited Nellore
The water base limited Nellore-KCT Group2021.01-2022.01(a year)Nellore Dist., Andhra Pradesh, India** 1. Understanding customer needs and requirements to develop effective quality control processes. 2. Devising and reviewing specifications for products or processes. 3. Setting requirements for raw material or intermediate products for suppliers and monitoring their compliance. 4. Proactively identifying issues and providing general guidance to resolve QC operational issues. 5. Working with laboratory management to develop solutions to meet productivity/quality objectives. 6. Ensuring adherence to health and safety guidelines as well as legal obligations. 7. Supervising and guiding inspectors, technicians, and other staff and providing guidance and feedback. 8. Overseeing all product development procedures to identify deviations from quality standards. 9. Inspecting final output and comparing properties to requirements. 10. Approving the right products or rejecting defectives. 11. Keeping accurate documentation and performing statistical analysis and submitting reports. Achievements • Improved Product Quality: Reduced defects and enhanced product consistency through better inspection and standardized testing. • Regulatory Compliance: Ensured full compliance with ISO, GMP, HACCP, and industry standards; supported successful audits with accurate documentation. • Efficient Lab Operations: Increased testing accuracy and reduced turnaround time by improving lab workflows and equipment calibration. • Corrective & Preventive Actions: Led or supported effective CAPA processes, minimizing repeat issues and managing non-conformances efficiently. • Process & SOP Improvement: Updated and optimized SOPs, improving team efficiency and adherence to quality standards. • Cross Department Support: Collaborated with production teams to resolve quality issues quickly, reducing downtime and material waste. • Customer Satisfaction: Lower quality-related complaints by identifying root causes and driving continuous improvement. • Training & Development: Trained QC staff and operators on quality procedures, boosting knowledge and performance.Deputy Quality Assurance
Royals Marine Food Pvt. Ltd., Guntur Dist., Andhra Pradesh, India.2019.01-2021.01(2 years)/Quality Control (QA/QC) Manager - Royals Marine Food Pvt. Ltd., Guntur Dist., Andhra Pradesh, India** 1. Overseeing and managing all aspects of quality assurance and quality control within an organization. 2. Developing, implementing, and maintaining quality management systems, policies, and procedures to ensure compliance with quality standards and regulatory requirements. 3. Setting quality objectives and targets, monitoring quality performance metrics, and driving continuous improvement initiatives. 4. Working closely with cross-functional teams to optimize processes, resolve quality issues, and enhance product quality and customer satisfaction. 5. Contributing and working closely with relevant teams for future improvements and/or systems enhancement. 6. Validation and quality control of new system and perform testing depends on regular hot fix patch of multi retail systems. 7. Managing the implementation/deployment of system enhancements/new systems through the project life cycle. 8. Building organizational strength and knowledge of science and Lab systems generally attained through studies resulting in a B.S 9. Being certified as Lead Auditor of Quality Management System as per ISO 19011. 10. Leading workplace safety through prevention, instruction, and random inspection. 11. Monitoring prime and subcontract actions for contract compliance, monitors risk and contributes suggestions for risk mitigation. Achievements • Enhanced Quality Systems: Improved QA/QC procedures, reducing defects and increasing audit readiness. • Regulatory Compliance: Maintained full compliance with standards like ISO, GMP, and HACCP; passed audits with minimal findings. • CAPA Leadership: Led corrective and preventive actions, reducing recurring quality issues and customer complaints. • Lab Efficiency: Boosted accuracy and speed of lab testing through workflow optimization and equipment calibration. • Process Improvement: Updated SOPs and monitored key quality metrics (KPIs) to drive continuous improvement. • Team Development: Trained and supported QA/QC staff, improving overall team performance and technical skills. • Cross-Functional Collaboration: Worked closely with production and other departments to resolve quality issues efficiently. • Customer Satisfaction: Decreased complaints and successfully handled customer audits through proactive quality management. July’ 2016 – Aug’ 2019 ** Senior Executive-Quality Control (QC) and Quality Assurance (QA) -Deepak NexGen Feeds and Foods Pvt. Ltd., Krishna Dist. Andhra Pradesh, India** 1. Develop, implement, and maintain quality assurance protocols and procedures. 2. Oversee quality control activities, including inspections and testing of raw materials, in-process products, and finished goods. 3. Ensure compliance with industry standards and regulatory requirements. 4. Drive and manage quality and food safety processes, systems and guidelines for all incoming materials, processes as well as finished goods. 5. Identify and target key accounts for business development. 6. Negotiate contracts and agreements with key accounts. 7. Develop and implement sales strategies to achieve targets. 8. Monitor and analyze sales performance. 9. Provide regular updates and reports to management. 10. Collaborate with cross-functional teams to ensure customer satisfaction. 11. Stay updated on industry trends and competitors Achievements • Regulatory Compliance: Ensured full compliance with ISO, GMP, HACCP, and other quality standards; supported successful audits. • Testing Efficiency: Improved lab accuracy and reduced testing turnaround times through better processes and equipment calibration. • CAPA Implementation: Led or supported corrective and preventive actions, reducing repeat quality issues and customer complaints. • Defect Reduction: Helped lower product defects through in-process inspections and quality monitoring. • SOP & Training: Ensured SOP compliance and trained staff on quality procedures, GMP, and safety standards. • Customer Satisfaction: Contributed to handling and resolving complaints, supporting product and process improvements. Key Functional Roles 1. Operational Excellence: Across departments, there was a significant improvement in operational efficiency, production output, and cost management through cross-functional collaboration and process optimization. 2. Quality & Compliance: All managers contributed to achieving or maintaining critical certifications (ISO, FDA, etc.), ensuring compliance with industry standards and reducing defects and non-compliance. 3. Innovation: Led new product innovations, including healthier and more sustainable products, aligning with changing consumer preferences and dietary needs. 4. Customer-Centric Approach: A customer-first mindset was established across the teams, resulting in reduced complaints, faster response times, and products that better met consumer demands. 5. Sustainability: Across all departments, sustainability efforts were a priority, with reduced waste, energy efficiency, and sustainable sourcing contributing to both cost savings and corporate social responsibility goals. 6. Oversee daily operations in the Animal feed sector. 7. Develop and implement operational strategies. 8. Manage budgets and ensure cost-effectiveness. 9. Ensure compliance with industry regulations. 10. Analyze and improve operational processes. 11. Manage a diverse team of employees. 12. Work closely with other departments. 13. Ensure products are delivered on time. 14. Overseeing the day-to-day operations of the manufacturing facility. 15. Ensuring that production targets are met, quality standards are maintained, and operational efficiency is optimized. 16. Collaborating with various departments, such as production, logistics, and quality control, to ensure smooth operations and timely delivery of products. 17. Analyzing production data, identifying areas for improvement, and implementing strategies to enhance productivity and reduce costs. 18. Managing a team of supervisors and ensuring compliance with safety regulations and company policies and to ensure that all products within a company meet consistent standards and develop and implement quality control tests to ensure the company’s result is what it should be, inspecting at various stages in production and writing reports on their findings to take action where needed and the goal is to help preserve the company's reputation by ensuring that its products and services are capable to drive sustainable growth. 19. Customer Complaints Handling Corrective Actions (CA) • Quick Resolution: Reduced complaint resolution time by streamlining processes, ensuring faster responses to feed-related issues. • Root Cause Identification: Identified recurring issues (e.g., contamination, nutritional imbalances) and implemented targeted solutions. • Product Adjustments: Improved feed formulations or packaging based on customer feedback (e.g., adjustingprotein content, addressing allergen concerns). • Customer Retention: Increased satisfaction by resolving complaints efficiently, turning negative experiences into positive ones. • Team Training: Trained teams manage complaints effectively, reducing future occurrences of the same issues. Preventive Actions (PA) • Root Cause Elimination: Addressed systemic issues (e.g., ingredient inconsistencies) to reduce future complaints. • Improved Quality Control: Enhanced production processes and feed formulations to prevent defects and nutritional inconsistencies. • Process Standardization: Established standardized procedures across production, quality, and packaging to prevent recurrence. • Supplier Collaboration: Strengthened supplier relationships to ensure consistent, high-quality raw materials. • Customer Education: Improved communication on feed composition, nutritional benefits, and proper usage to avoid misunderstandings. Types of Customer Complaints & Actions 1. Feed Quality Issues (CA: Replace contaminated batches, offer compensation and PA: Improve ingredientsourcing and quality control processes.) 2. Late Deliveries (CA: Expedite delivery, provide compensation and PA: Enhance logistics and supply chain) management. 3. Incorrect Labeling or Nutritional Information (CA: Re-label or recall products and PA: Strengthen labelingprocesses and regulatory compliance.) 4. Packaging Problems (CA: Repackage and replace damaged goods and PA: Improve packaging materials andpacking line checks.) 5. Poor Animal Performance (A: Replace feed or offer alternatives and PA: Reformulate feed based on expertfeedback.)
Languages
English
Skilled
Files
Resume Search
Nationality
Job category
City or country
Sort by
Contact way
91****3770
ja**@**om

Membership will unlock the resume
Also view